The Building Blocks of Strength
From steel giants to concrete foundations, various materials play crucial roles in construction. But why are these materials chosen for specific applications? Let’s delve into some of the most common:
- Metals: Steel, renowned for its strength-to-weight ratio, forms the backbone of many structures due to its durability and flexibility. Inspectors meticulously assess factors like corrosion, weld quality, and material defects to guarantee a building’s safety.
- Concrete: This composite of cement, aggregate, and water is preferred for its compressive strength, making it ideal for walls and foundations. Inspections focus on mix proportions, curing (hardening process), and identifying cracks that could compromise structural integrity.
- Wood: A traditional material known for its versatility and aesthetic appeal, wood is often used in residential construction where design flexibility is desired. Wood requires close inspection for moisture content, grain orientation, and signs of rot or warping.
- Composites: Engineered materials like fiber-reinforced polymers (FRP) offer high strength-to-weight ratios and corrosion resistance, making them suitable for specialized applications.
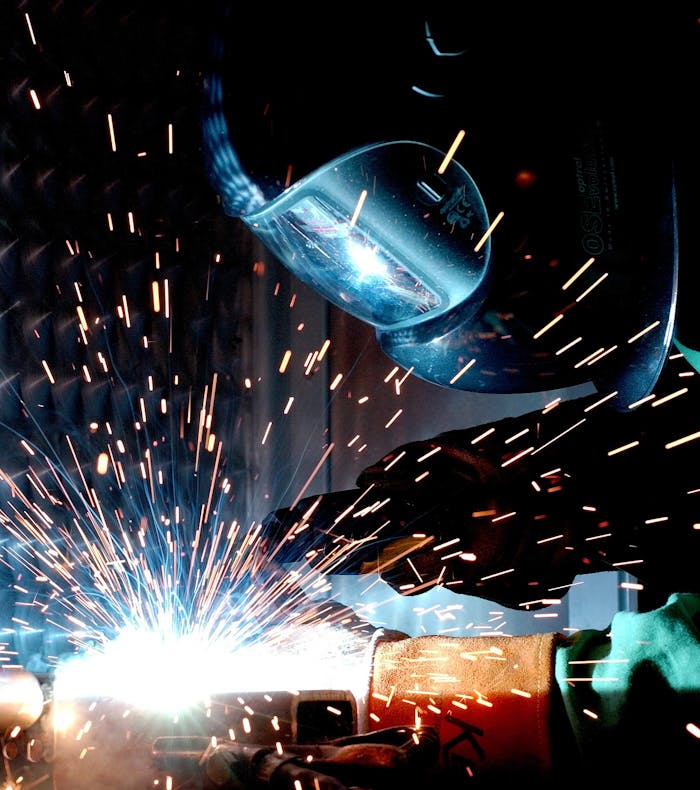
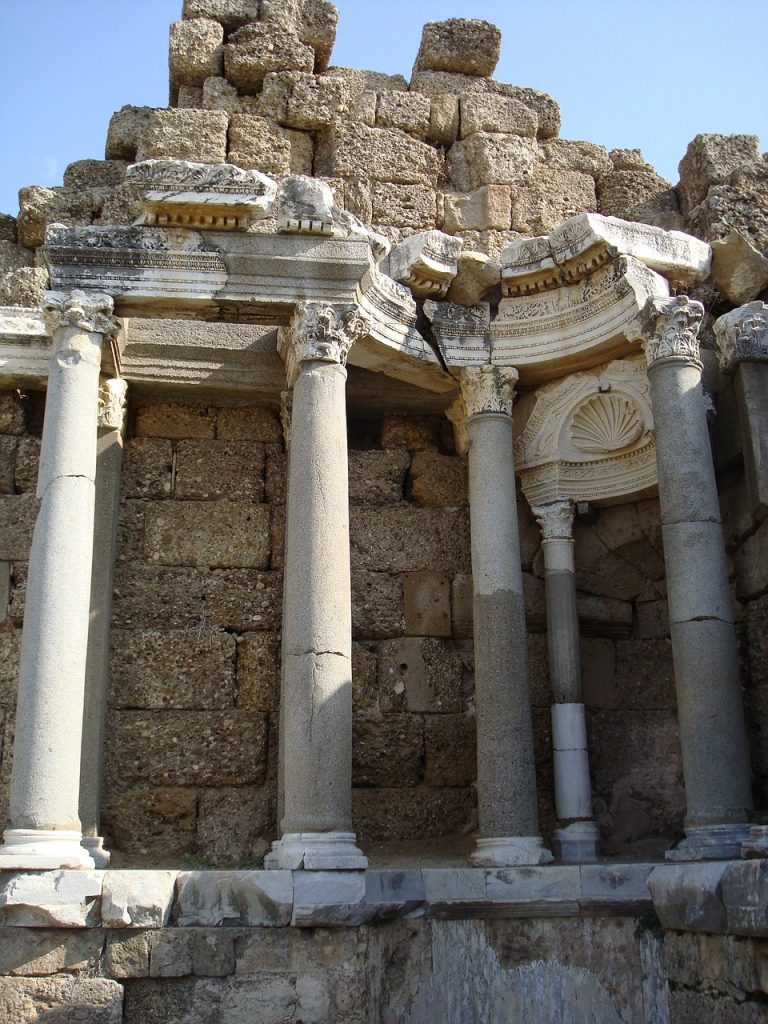
The Silent Threats
Over time, various defects can develop in structural materials due to storage, environmental factors, wear, or improper installation. Recognizing these red flags is crucial:
- Corrosion in Metals: Rust and other corrosion products weaken steel. Look for discoloration, pitting, or reduced thickness.
- Cracking in Concrete: Cracks allow water ingress and can compromise structural integrity. They can be caused by shrinkage, thermal expansion, or overloading.
- Warping and Rot in Wood: Changes in moisture content, insects, and fungal decay can distort wood and reduce its load-bearing capacity. Signs include discoloration, softening, and warping.
- Delamination in Composites: When layers separate in FRP or laminates, their strength and performance diminish. Look for visible cracks, blisters, or delamination.
Unveiling the Invisible
- Several methods are employed to assess the condition of structural materials:
- Visual Inspection: The most basic method, it involves examining surfaces for irregularities, defects, and signs of deterioration.
- Non-Destructive Testing (NDT): Techniques like ultrasonic and radiographic testing evaluate materials without damaging them.
- Destructive Testing: Involves subjecting samples to controlled stress to assess their mechanical properties and failure characteristics.
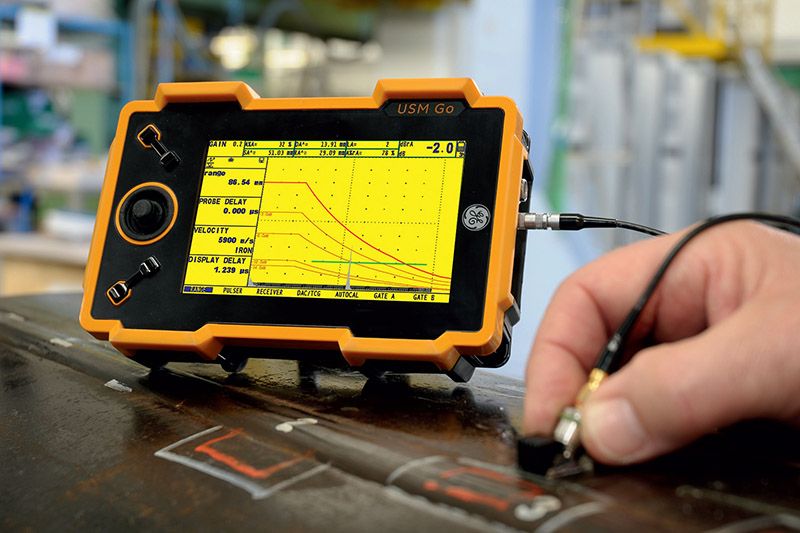
Ultrasonic Testing Machine
The Power of Materials Traceability
Tracking materials throughout their lifecycle, from sourcing to installation, is crucial for quality control. This “materials traceability” ensures:
- Verification of Authenticity: Materials meet the specified grade, quality, and standards.
- Prevention of Errors: Improper materials can be identified and replaced.
- Improved Project Safety: Traceability helps pinpoint potential issues before they become major problems.
Advanced technologies like RFID tags and QR codes are revolutionizing materials traceability, allowing for real-time tracking and data collection.
Building a Safe and Sustainable Future
Rigorous structural materials inspection is the cornerstone of safe and sustainable construction. By employing various inspection methods and robust materials traceability practices, we can ensure the buildings we inhabit remain strong and secure for generations to come.
What are your thoughts on the importance of structural materials inspection? Share your experiences or questions in the comments below!
#structuralengineering #construction #materials #inspection #safety #engineering